Name of Project: SR-24 Asphalt Rehabilitation & Shoulders Project
Project Location: Wayne County, Utah
Project Start: March 2022
Project Completion: November 2022
Key Project Team Members:
- UDOT — Project Owner
- Nielson Construction & Materials — General Contractor
- Eric Luke — Project Manager
- Mike Ziemski — Superintendent
- Harward & Rees — Key Subcontractor
- Horizon Environmental — Key Subcontractor
- American Traffic Services — Key Subcontractor
Tons of Asphalt Placed: 33,000 tons of HMA, 51,000 tons of SMA
Project Overview
The project is in Wayne County, Utah. The project starts in Loa and ends outside of Hanksville. This route is designated as a National Scenic Byway and is the primary access to Capitol Reef National Park. The project is approximately 33 miles in length and winds through picturesque red rock cliffs of Capitol Reef. The route is very popular with tourists and hikers, which created unique traffic challenges to overcome during construction. The scope of the project consisted of shoulder widenings, lane leveling HMA and an SMA overlay. The paving totaled 33,000 tons of HMA, 51,000 tons of SMA. 65,000 CY of excavation, and 35,000 ton of gravel import to construct shoulder widenings on the project.
What Makes the Project Unique
The shoulder widenings presented unique challenges due to the limited project right of way. The design team was challenged to maximize shoulder width to accommodate visitor traffic without encroaching on the natural environment. The resulting design was one of sliver cuts and sliver fills. This was very technical work performed in extremely tight areas.
Inside National Park boundaries, the construction team successfully worked around highly sensitive environmental, archaeological, and paleontological sites.
Safety Record on the Project
The safety performance on the project was great. With over 76,000 hours worked, only two recordable incidents occurred. The first was a water truck backing into an asphalt roller resulting in a slight paint exchange, and the second involved a tack distributor backing into a pick-up resulting in minor damage to both vehicles. We are happy to report that there were zero accidents involving the traveling public on the project.
Our company uses multiple safety programs to ensure safe work practices. These programs include Tyfoom, where employees watch daily safety videos and complete a short quiz; TRACK, which is a risk management tool completed at the start of each new task; and all employees are empowered to stop work through See-Stop-Do — when they see something, they are empowered to stop work and correct the hazard. Employees are also trained on LSRs (Life Saving Rules), which provide training on high risk activities monthly.
In addition, a project Public Information Officer was employed full time on the project. This had a positive impact as he was able to provide regular updates to the public including changes to traffic flow and a description of ongoing work.
OSHA incident rate — 0
Recordable incidents vs. man hours — 2 vs. 76,000 hours worked
Lost time accidents — 0
EMR — 0.52
Project Quality
Harward & Rees performed high quality work while completing the excavation work. They successfully walked a thin line of staying within project boundaries, managing concerns of the park biologist, working with a full-time paleontologist to identify uncovered fossils, and a tight project schedule while providing a high quality of work.
In recent years, Capitol Reef has experienced regular flash flooding. While not included in the original scope of work, additional drainage concerns were identified by the team. Additional culverts were added to help mitigate recent flooding issues adding to the quality of the project and mitigating future maintenance for the park service.
Also adding to the quality of the delivered project was the use of stone matrix asphalt for the final surface on the project. The choice to utilize this type of asphalt mix greatly increases the initial wear life of the roadway and reducing the impacts to visitors to the park by reducing future pavement maintenance work.
All that travel the state’s highways either enjoy or complain about the smoothness of the pavement. A pre-paving profilograph was completed revealing how ruff this section of SR-24 was. With an MRI reading of >175, it placed the highway into UDOT’s roughest category. The quality of the work performed by the paving crews was exceptional as they reduced the MRI on the project from > 175 to < 65. This is an excellent improvement of 63% in ride quality.
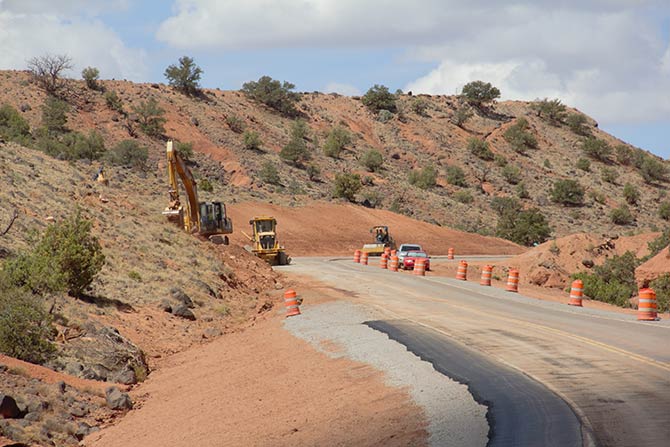
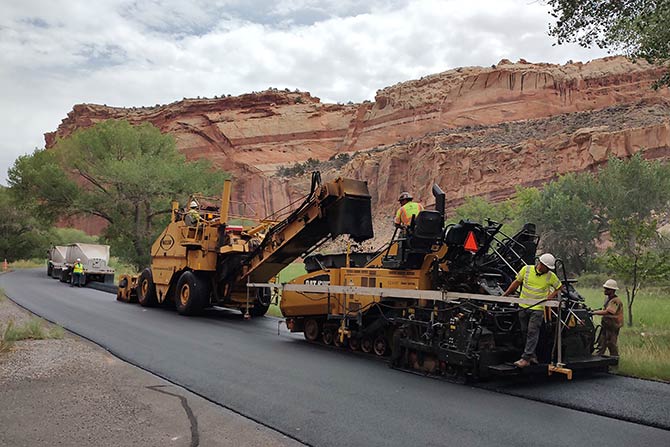
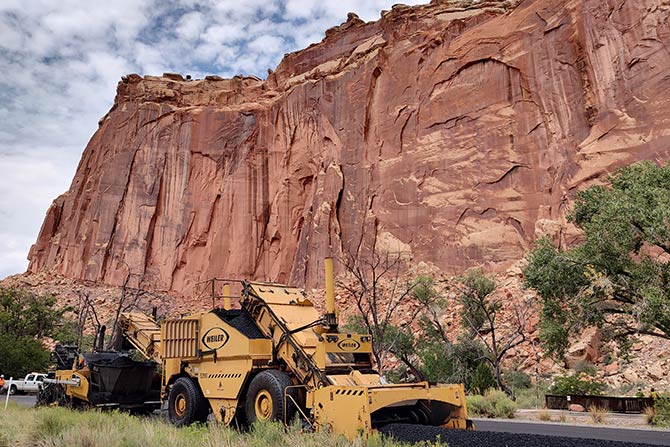